Organic agriculture is growing rapidly around the world, and small-scale organic fertilizer production lines are becoming increasingly popular among individual farmers, cooperatives, and agri-entrepreneurs. Unlike large industrial facilities, small-scale fertilizer production lines require less capital investment and infrastructure while still providing an efficient solution for recycling organic waste into valuable fertilizer products.
In this article, we will cover everything you need to know about building a small-scale organic fertilizer production line, including required equipment, raw materials, processing steps, space requirements, estimated budget, and profitability projections.
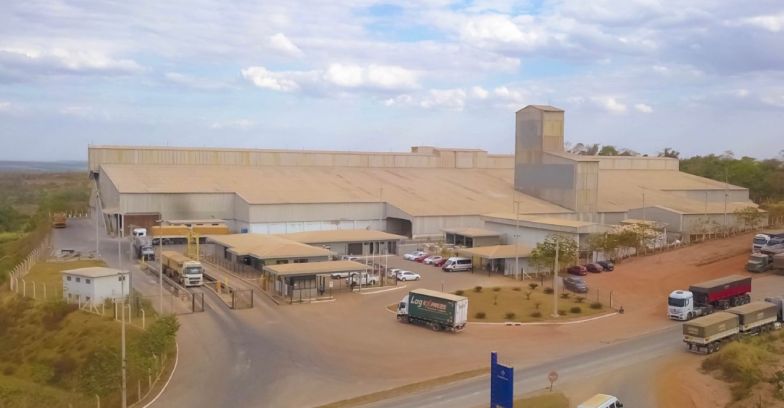
1. Why Start a Small-Scale Organic Fertilizer Plant?
1.1 Growing Demand for Organic Products
The demand for organic fruits, vegetables, and crops continues to rise, leading to increased need for certified organic fertilizers.
1.2 Waste Management Solution
Agricultural waste, animal manure, kitchen waste, and garden residues can all be converted into fertilizer, solving local waste disposal challenges.
1.3 Low Initial Investment
Small-scale setups require relatively modest capital outlay and infrastructure.
1.4 Local Market Opportunities
Farmers, nurseries, and urban gardens provide an immediate market for small-batch organic fertilizers.
1.5 Sustainable Income Source
Turn waste into profit by producing organic fertilizer year-round.
2. Typical Capacity of a Small-Scale Plant
Most small-scale organic fertilizer lines have an annual capacity of:
- 500 to 5,000 tons/year
- Equivalent to 1–15 tons/day of input material (depending on moisture and composition)
This capacity is ideal for individual farms, small cooperatives, or localized production hubs.
3. Essential Equipment for Small-Scale Production
Here is a list of basic machinery required for a complete small-scale organic fertilizer line:
3.1 Compost Turner (Optional but Recommended)
- For aerobic fermentation of raw organic materials
- Types: Windrow turner (preferred), manual fork or small self-propelled turner
3.2 Crusher (Pre-Treatment)
- Breaks down composted material lumps
- Ensures uniform granule size
3.3 Mixer
- Mixes base compost with additives like NPK, zeolite, or humic acid
3.4 Granulator
- Converts powdered compost into granular form for easier packaging and application
- Options: Disc granulator (ideal for small scale), pan granulator
3.5 Dryer & Cooler (Optional)
- Removes excess moisture and improves shelf life
- Not always needed for low-volume or local sales
3.6 Screener
- Separates fine or oversized materials
- Ensures uniform product appearance
3.7 Packing Machine
- Semi-automatic or manual bagging solutions
- Packaging sizes: 10kg, 25kg, 50kg, etc. (Related post: organic fertilizer production project)
4. Suitable Raw Materials
You can choose one or a combination of the following:
- Chicken manure
- Cow dung
- Pig manure
- Sheep manure
- Mushroom residue
- Crop straw
- Kitchen waste
- Municipal organic waste
- Slaughterhouse waste (with proper treatment)
The Carbon to Nitrogen (C:N) ratio should ideally be around 25–30:1 for optimal composting.
5. Production Process Flow
- Raw Material Collection: Animal waste, plant waste, etc.
- Composting: Aerobic fermentation for 15–25 days with regular turning
- Crushing: Reduces size and breaks clumps
- Mixing: Homogenizes compost and additives
- Granulating: Forms round or irregular granules
- Drying & Cooling (if required)
- Screening: Filters oversize/undersize particles
- Packaging: Final product is bagged and stored for sale
6. Space and Infrastructure Requirements
A small-scale plant can fit in an area of 200–1,000 square meters, depending on layout and storage needs.
Basic requirements:
- A covered workshop for equipment and operations
- Open space for composting (if windrow system is used)
- Electricity and water supply
- Storage area for raw materials and finished products
7. Budget Estimation for a Small-Scale Organic Fertilizer Plant
Component | Estimated Cost (USD) |
---|---|
Compost Turner | $3,000 – $10,000 |
Crusher | $2,000 – $5,000 |
Mixer | $1,500 – $3,000 |
Granulator | $3,000 – $8,000 |
Dryer & Cooler (Optional) | $8,000 – $15,000 |
Screener | $2,000 – $4,000 |
Packing Machine | $1,000 – $3,000 |
Installation & Setup | $5,000 – $10,000 |
Total | $20,000 – $60,000 |
Note: Costs vary by region, brand, and equipment configuration.
8. Operating Costs
Monthly operating expenses may include:
- Labor (1–3 operators)
- Electricity & water
- Maintenance
- Packaging material
- Transportation (if delivering products)
Estimated monthly operational cost: $2,000–$5,000
9. Potential Revenue and Profitability
Assume:
- Production: 2,000 tons/year
- Selling price: $80–$120/ton
- Annual revenue: $160,000–$240,000
- Net profit (after costs): $40,000–$80,000/year
Profitability improves with direct sales to farmers, cooperatives, or via retail. (Related post: fertilizer granulator machine)
10. Marketing Strategies
To boost sales:
- Partner with local farmers’ markets or garden centers
- Offer free samples to nearby farms
- Use social media and content marketing
- Educate buyers about the benefits of organic fertilizer
- Obtain organic certification (if selling to premium markets)
11. Environmental and Social Benefits
- Reduces organic waste pollution
- Enhances soil fertility and crop yields
- Minimizes use of synthetic fertilizers
- Encourages sustainable agriculture in your community
12. Common Mistakes to Avoid
- Skipping composting: Leads to immature fertilizer, odor, and pathogen issues
- Wrong C:N ratio: Poor composting results
- Overestimating capacity: Start small and scale up as demand grows
- Neglecting quality control: Granule size and nutrient consistency matter
13. Real-World Examples
Case Study: Kenya Small Farm Co-op
- Capacity: 1,500 tons/year
- Investment: $30,000
- Payback time: 18 months
- Outcome: Selling directly to 300+ farmers
Case Study: Peru Urban Garden Project
- Capacity: 800 tons/year
- Uses municipal kitchen and garden waste
- Partnered with city council for supply and distribution
14. Conclusion
Starting a small-scale organic fertilizer production line is a practical and profitable way to recycle organic waste and contribute to sustainable agriculture. With the right equipment, local market knowledge, and commitment to quality, even modest operations can generate strong income while positively impacting the environment.