1. Introduction
Organic fertilizer pellet machines play a vital role in the production of organic fertilizers. However, during their operation, these machines often generate significant noise, which not only creates an unpleasant working environment for operators but also may cause noise pollution in the surrounding areas. Understanding the causes of this noise and implementing effective noise – reduction measures are crucial for improving the working conditions and environmental friendliness of organic fertilizer production facilities. This article comprehensively analyzes the reasons for noise generation in organic fertilizer pellet machines and proposes corresponding noise – reduction measures.
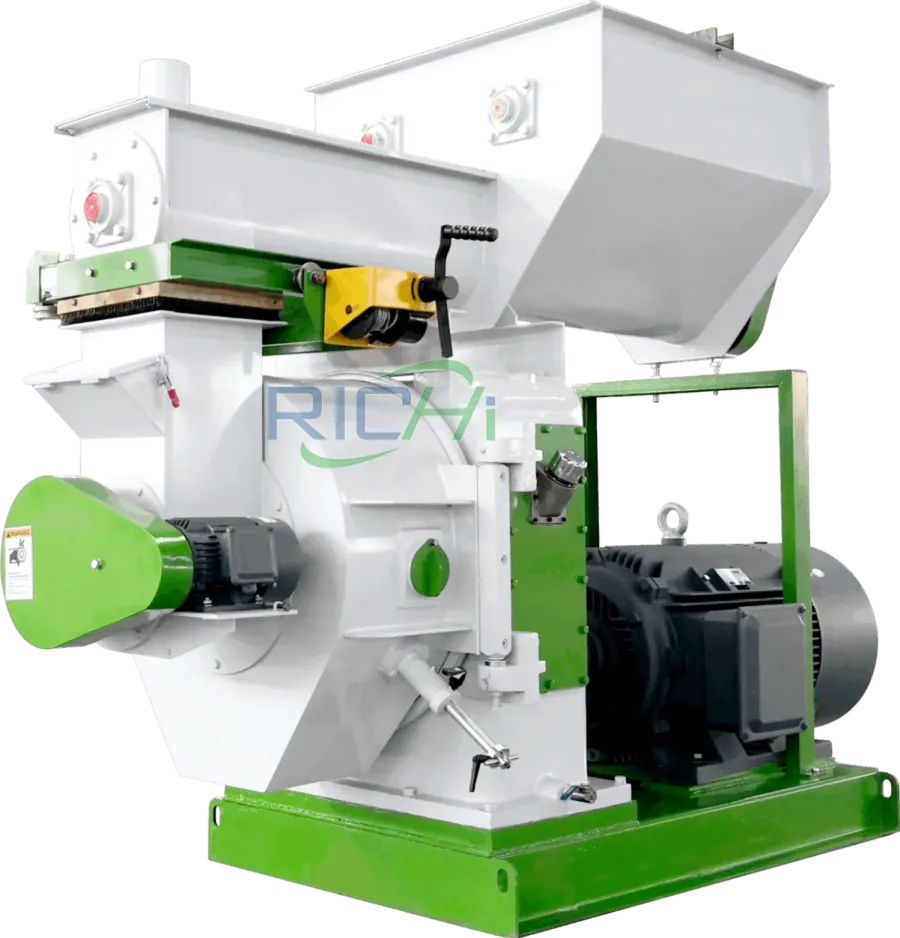
2. Importance of Addressing Noise in Organic Fertilizer Pellet Machines
2.1 Operator Health and Safety
Excessive noise exposure can have a negative impact on the health of machine operators. Prolonged exposure to high – intensity noise can lead to hearing loss, tinnitus, and other auditory problems. In addition, noise can also cause stress, fatigue, and distraction, increasing the risk of accidents in the workplace. For example, if an operator cannot clearly hear warning signals due to the loud noise of the pellet machine, it may lead to equipment malfunctions or safety incidents.
2.2 Environmental Protection
Noise pollution is a significant environmental concern. High – noise – generating organic fertilizer pellet machines can disrupt the peace and quiet of the surrounding residential and natural areas. In agricultural production areas that are close to residential communities, the noise from pellet machines may cause discomfort to local residents, leading to potential complaints and conflicts. Therefore, reducing the noise of organic fertilizer pellet machines is an important part of environmental protection in the agricultural production process.
2.3 Equipment Performance and Longevity
Excessive noise may also be an indication of abnormal operation or mechanical problems in the organic fertilizer pellet machine. By addressing the noise issue, potential equipment failures can be detected and resolved in a timely manner. For example, unusual noises from bearings or gears may suggest wear and tear, and taking appropriate measures to reduce noise can also extend the service life of the equipment and improve its overall performance.
3. Reasons for Noise Generation in Organic Fertilizer Pellet Machines
3.1 Mechanical Vibration
Unbalanced Rotating Parts
Many organic fertilizer pellet machines, such as compression pelletizers with rotating rollers and extrusion pelletizers with screws, have rotating parts. If these parts are not properly balanced during manufacturing or installation, they will generate centrifugal forces during rotation, resulting in mechanical vibration and noise. For example, if the rollers in a compression pelletizer are not balanced, the uneven distribution of mass will cause the rollers to vibrate as they rotate, generating noise in the range of 80 – 100 decibels (dB).
Loose or Worn – Out Components
Over time, components of the pellet machine, such as bolts, nuts, and bearings, may become loose or worn out. Loose components can rattle and produce noise during machine operation. Worn – out bearings, in particular, can cause significant noise due to increased friction and uneven rotation. For instance, a worn – out bearing in the drive system of an organic fertilizer pellet machine can generate a high – pitched screeching noise, which can be as loud as 110 – 120 dB. (Related post: Organic Fertilizer Production Line)
3.2 Friction and Impact
Friction between Moving Parts
In the operation of organic fertilizer pellet machines, there are numerous moving parts that are in contact with each other, such as the rollers and dies in compression pelletizers, and the screw and barrel in extrusion pelletizers. The friction between these parts during operation can generate noise. The type of materials used, surface roughness, and the presence of lubrication all affect the level of frictional noise. For example, if the die surface in a compression pelletizer is too rough, the friction between the rollers and the die will increase, resulting in louder noise.
Impact during Material Processing
When organic raw materials are processed in the pellet machine, impact forces are generated. In compression pelletizers, the raw materials are compressed and forced through the die holes, causing impact between the materials and the die. In disc pelletizers, the materials are tossed and tumbled on the rotating disc, resulting in impacts between particles and the disc surface. These impact – related noises can be sharp and intermittent, contributing to the overall high – noise level of the machine.
3.3 Aerodynamic Factors
Airflow – Related Noise in Ventilation Systems
Many organic fertilizer pellet machines are equipped with ventilation systems to dissipate heat and remove dust. However, the high – speed airflow in these ventilation systems can generate noise. The design of the ducts, the speed of the fans, and the presence of obstructions in the airflow path all affect the noise level. For example, if the fan blades in the ventilation system are not properly designed or installed, they can cause turbulence in the airflow, resulting in aerodynamic noise in the range of 70 – 90 dB.
Noise from Exhaust Gases (if applicable)
In some cases, such as in pellet machines with heating systems for drying raw materials, the exhaust gases can also generate noise when they are discharged. The pressure and velocity of the exhaust gases, as well as the design of the exhaust pipes, play important roles in determining the noise level. High – pressure and high – velocity exhaust gases can produce loud hissing or roaring noises.
4. Noise – Reduction Measures for Organic Fertilizer Pellet Machines
4.1 Mechanical Optimization
Balancing Rotating Parts
To address the problem of unbalanced rotating parts, strict quality control measures should be implemented during the manufacturing and installation of organic fertilizer pellet machines. Rotating parts, such as rollers and screws, should be carefully balanced using professional balancing equipment. This can significantly reduce the mechanical vibration and noise generated during operation. For example, after balancing the rollers in a compression pelletizer, the noise level can be reduced by 10 – 15 dB.
Regular Component Inspection and Replacement
Regular inspection of machine components is essential. Loose bolts and nuts should be tightened in a timely manner, and worn – out components, such as bearings and gears, should be replaced. Implementing a preventive maintenance program can help detect potential problems early. For instance, by replacing worn – out bearings every six months (depending on the usage frequency of the machine), the noise caused by bearing wear can be effectively reduced.
4.2 Friction and Impact Mitigation
Lubrication Optimization
Proper lubrication of moving parts is crucial for reducing friction and noise. Selecting the appropriate lubricants according to the operating conditions of the machine, such as high – temperature – resistant lubricants for parts operating at high temperatures, can significantly reduce frictional noise. In addition, the lubrication frequency should be optimized. For example, for the rollers and dies in a compression pelletizer, lubricating them once a week can effectively reduce friction and noise.
Design Modifications to Reduce Impact
The design of the granulation chamber and related parts can be modified to reduce the impact during material processing. For example, in compression pelletizers, the shape of the die holes can be optimized to make the material extrusion process more smooth, reducing the impact force. In disc pelletizers, adding soft – lining materials on the disc surface can reduce the impact noise when the materials are tossed on the disc. (Related case:10-12T/H Organic Fertilizer Production Plant In Ecuador)
4.3 Aerodynamic Noise Control
Ventilation System Optimization
The ventilation system of the organic fertilizer pellet machine can be optimized to reduce aerodynamic noise. This includes using ducts with smooth inner surfaces to reduce airflow turbulence, selecting fans with low – noise designs, and ensuring proper installation of the ventilation components. For example, replacing a standard fan with a high – efficiency, low – noise fan can reduce the ventilation – related noise by 10 – 20 dB.
Exhaust – Gas Noise Suppression
If there are exhaust – gas – related noises, installing noise – suppression devices, such as mufflers, in the exhaust pipes can be an effective solution. Mufflers work by dissipating the energy of the exhaust gases through absorption, reflection, or interference, reducing the noise level. The design and size of the muffler should be selected according to the characteristics of the exhaust gases, such as pressure, velocity, and volume.
4.4 Acoustic Enclosures and Insulation
Installing Acoustic Enclosures
Constructing acoustic enclosures around the organic fertilizer pellet machine can effectively reduce noise propagation. Acoustic enclosures are typically made of sound – absorbing materials, such as fiberglass, mineral wool, or acoustic foam. These materials can absorb and reflect sound waves, reducing the noise level in the surrounding area. For example, an acoustic enclosure can reduce the noise level of a pellet machine by 20 – 30 dB.
Using Sound – Insulating Materials in Machine Design
In the design of the organic fertilizer pellet machine itself, sound – insulating materials can be used in the construction of the machine housing and other components. For example, using double – walled structures with sound – insulating materials in the middle can enhance the sound – insulation performance of the machine. This can not only reduce the noise emitted by the machine but also improve the overall acoustic environment in the production area.
5. Case Studies of Noise – Reduction in Organic Fertilizer Pellet Machines
5.1 Case 1: A Small – Scale Organic Fertilizer Producer
A small – scale organic fertilizer producer was troubled by the high noise of its compression pelletizer. After inspection, it was found that the rollers were unbalanced, and the bearings were worn out. The producer first balanced the rollers using a professional balancing machine and then replaced the worn – out bearings. In addition, the producer installed an acoustic enclosure around the pelletizer. After these measures were taken, the noise level of the pelletizer decreased from about 105 dB to 75 dB, significantly improving the working environment for the operators.
5.2 Case 2: A Medium – Sized Organic Fertilizer Plant
A medium – sized organic fertilizer plant optimized the ventilation system of its extrusion pelletizer. The original ventilation system had ducts with rough inner surfaces and a high – speed fan that generated a lot of noise. The plant replaced the ducts with smooth – surface ducts and installed a low – noise fan. At the same time, the plant used sound – insulating materials to improve the machine housing. As a result, the overall noise level of the extrusion pelletizer decreased by about 25 dB, reducing the noise pollution in the surrounding area.
6. Conclusion
In conclusion, noise generation in organic fertilizer pellet machines is a multi – faceted problem caused by mechanical vibration, friction and impact, and aerodynamic factors. However, through a series of targeted noise – reduction measures, such as mechanical optimization, friction and impact mitigation, aerodynamic noise control, and the use of acoustic enclosures and insulation, the noise level of organic fertilizer pellet machines can be effectively reduced. Case studies have demonstrated the practical effectiveness of these measures. In the future, with the continuous improvement of technology and the increasing emphasis on environmental protection and operator health, more advanced noise – reduction technologies for organic fertilizer pellet machines are expected to emerge.