A 20 t/h animal feed milling machine is engineered to efficiently produce a substantial volume of high-quality animal feed pellets. These machines are crucial for the livestock and poultry sectors, where consistent and nutritious feed is essential for animal health and productivity. Understanding the main components of a 20 t/h animal feed milling machine is vital for operators and managers to ensure smooth operations and optimal output. This article outlines the key components of such a machine and their functions in the feed production process.
1. Crushing Machine
The crushing machine is the initial step in the animal feed production process. It is responsible for reducing the size of raw materials, such as grains, legumes, and other feed ingredients.
- Function: Typically a hammer mill, the crushing machine grinds raw materials into smaller particles, facilitating easier mixing and processing in subsequent steps. This size reduction is critical for achieving uniformity in the final feed product.
- Importance: Properly crushed materials enhance the efficiency of mixing and pelleting processes, resulting in better feed quality and digestibility for the animals.
2. Mixing Machine
After crushing, the raw materials must be mixed thoroughly to ensure an even distribution of nutrients.
- Function: The mixing machine combines various feed ingredients, including grains, protein sources, vitamins, and minerals, ensuring uniform blending to create a consistent feed formulation.
- Types: Common types of mixers used in animal feed production include horizontal ribbon mixers and vertical mixers. The choice of mixer depends on specific feed formulation requirements and production capacity.
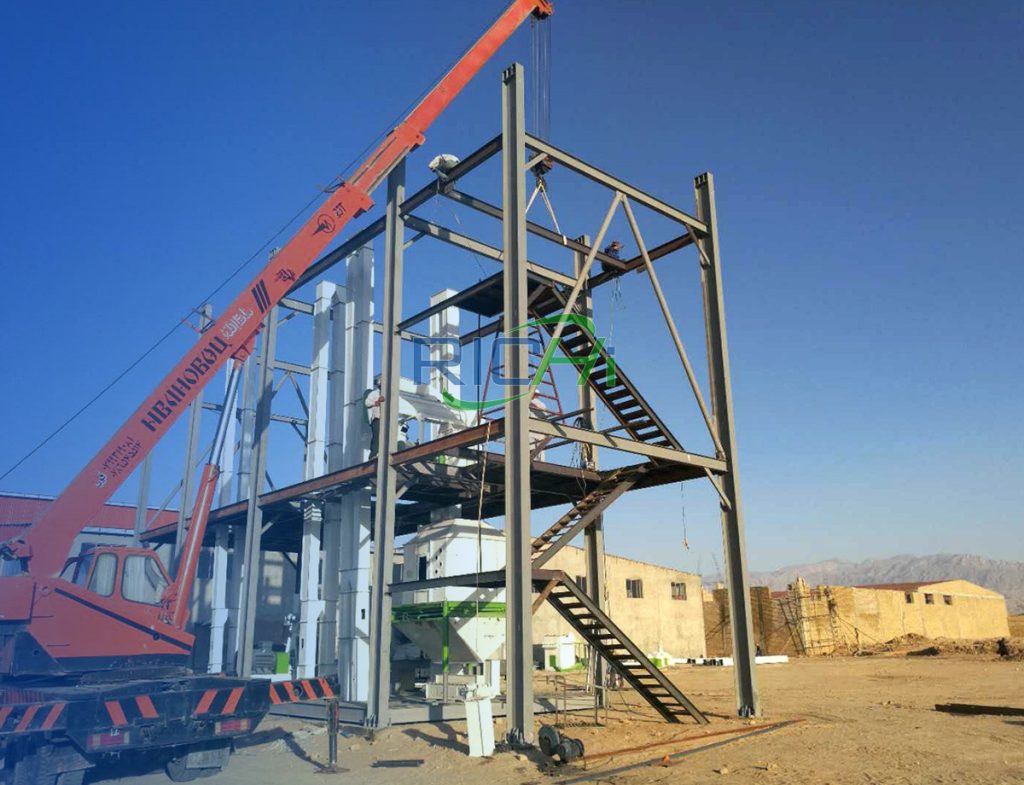
3. Pellet Mill
The pellet mill serves as the heart of the animal feed milling machine, where the actual pelleting process occurs.
- Function: The pellet mill compresses the mixed feed ingredients through a die using rollers, forming pellets. The heat and pressure generated during this process cause the materials to bind together, resulting in high-density pellets.
- Types of Pellet Mills: There are two main types of pellet mills: flat die and ring die. For a 20 t/h capacity, a ring die pellet mill is typically preferred due to its higher efficiency and production capabilities.
4. Conditioning Unit
The conditioning unit is an optional but beneficial component that enhances the pelleting process.
- Function: This unit adds steam or moisture to the feed mixture before it enters the pellet mill. Conditioning softens the raw materials, making them easier to compress and improving pellet quality.
- Benefits: Proper conditioning activates the natural binding agents in the feed ingredients, resulting in stronger and more durable pellets, while also reducing wear on the pellet mill components.
5. Cooling Machine
Once the pellets are formed, they need to be cooled to maintain their quality and prevent spoilage.
- Function: The cooling machine reduces the temperature of the hot pellets, allowing them to harden and stabilize. This step is essential for ensuring that the pellets retain their shape during storage and transportation.
- Types: Counter-flow coolers are commonly used in large-scale feed production. These coolers utilize ambient air to cool the pellets while allowing moisture to escape, ensuring a dry final product.
6. Screening Machine
The screening machine is responsible for ensuring the uniformity and quality of the final feed product.
- Function: This machine separates any fines (small particles) from the finished pellets, as fines can negatively impact the quality and marketability of the feed.
- Importance: By removing fines, the screening machine ensures that only high-quality pellets are packaged and sold, enhancing customer satisfaction and minimizing waste.
7. Packing Machine
Once the pellets have been cooled and screened, they are ready for packaging.
- Function: The packing machine fills bags or containers with the finished feed pellets for distribution, ensuring that the product is properly sealed and labeled for sale.
- Automation: Many modern packing machines are automated, allowing for quick and efficient packaging of large quantities of feed. This reduces labor costs and improves overall production efficiency.
8. Control System
The control system is a crucial component that oversees the operation of the entire feed milling machine.
- Function: This system monitors and controls various parameters, such as feed flow rates, temperatures, and pressures, ensuring optimal performance within specified limits.
- Automation: Advanced control systems may include programmable logic controllers (PLCs) and touch-screen interfaces, allowing for easy monitoring and adjustments during operation.
9. Dust Collection System
A dust collection system is vital for maintaining a clean and safe working environment in the feed production facility.
- Function: This system captures airborne dust generated during the grinding and pelleting processes, improving air quality and reducing the risk of fire hazards.
- Components: Dust collectors typically include filters and fans to remove dust particles from the air and prevent them from accumulating in the production area.
10. Conveyor Systems
Conveyor systems are essential for transporting raw materials and finished products throughout the feed production process.
- Function: These systems facilitate the movement of materials between different stages of production, such as from the mixer to the pellet mill and from the cooler to the packing machine.
- Types: Various types of conveyors can be utilized, including belt conveyors, screw conveyors, and bucket elevators. The choice of conveyor depends on the specific layout and requirements of the production facility.
Conclusion
A 20 t/h animal feed production machine consists of several key components, each playing a vital role in the production process. From the initial crushing of raw materials to the final packaging of finished pellets, understanding the functions and importance of each component is essential for operators and managers.
By ensuring that each part of the machine operates efficiently and effectively, businesses can enhance productivity, improve feed quality, and meet the growing demand for high-quality animal feed. As the livestock industry continues to expand, investing in a well-designed animal feed milling machine will be crucial for success in this competitive market.