In the production of extruded feed, the main equipment is a screw fish feed pellet extruder. The material is fed into the fish feed pellet extruder, and the screw screw pushes the material to form an axial flow.
At the same time, due to the mechanical friction between the screw and the material, the material and the barrel, and the material inside the material, the material is strongly squeezed, stirred, and sheared, and as a result, the material is further refined and homogenized.
As the pressure gradually increases, the temperature increases accordingly. When the paste material is ejected from the die hole, under the action of a strong pressure difference, the material is puffed by floating fish feed making machine, dehydrated and cooled. The puffed product is loose, porous, crisp, and has good palatability and flavor.
The fish feed pellet extruder puffing technology breaks through the traditional processing technology, makes the physical properties of the feed change qualitatively, greatly promotes the development of the feed processing industry and the breeding industry, and is a major innovation in the feed industry.
The fish feed pellet extruder puffing process is a process that integrates various operations such as mixing, kneading, shearing, heating, and cooling. The following is a specific analysis from the aspects of density control, automatic control and energy saving and consumption reduction.
1. Density control technology
In the extrusion process of fish feed pellet extruder, there are many factors that affect the density of feed, such as processing technology, fish feed pellet extruder equipment, processing parameters, process control, feed raw materials, formula and so on.
It is feasible to control the product density by changing the raw material or formula, but it has little application value; by changing the screw configuration, the density control of the extruded feed product can be realized, but the operation is inconvenient. Density control can also be achieved by adjusting the operating parameters.
In addition, in the fish feed pellet extruder processing of aquatic feed, in order to meet the feeding requirements of aquatic animals, the ups and downs of aquatic feed should be controlled, and the ups and downs of feed are closely related to density, so density control is applied in the production of aquatic extruded feed.
Technology is particularly important. At present, controlling the density of extruded products is mainly achieved by controlling the pressure and temperature. The main methods are as follows:
(1)Open a pressure relief hole on the extruding cavity, and plug the pressure relief hole when producing floating feed, so as to meet the needs of high temperature and high pressure for processing floating feed.
Open the pressure relief hole when feeding, so that when the material reaches the pressure relief hole, the pressure in the sleeve is partially released, and at the same time, some water vapor is also discharged from the pressure relief hole.
These materials are extruded by fish feed pellet extruder to the end of the extruding cavity and then compacted to obtain a heavy feed with high bulk density. This pressure relief hole can also be used to evacuate, so that the material loses part of the water vapor during the forced movement.
This fish feed pellet extruder process method realizes the control of the density of the extruded product by controlling the pressure in the extruding cavity, and the output will not be affected because the feeding amount does not need to be reduced.
(2) A pressure regulating device is added in the floating fish feed extruder machine (pressurization before the die) .The pressure regulation of the fish feed pellet extruder is to install a shut-off valve between the extrusion cavity and the discharge template to adjust the pressure difference between the extrusion cavity and the outside of the extrusion cavity.
(3)Pressure cutting technology (post-mold pressure). A new type of density control system was developed for aquafeed. This density control system of fish feed pellet extruder adopts pressurized cutting technology to maintain a certain positive pressure in the cutting chamber.
When the material enters the cutting chamber from the puffing chamber, since the boiling point of water increases with the pressure, the flash evaporation can be reduced to control the degree of expansion of the material, and the starch molecules are instantly solidified in the cutting chamber, and the material no longer enters the normal pressure from the cutting chamber.
The positive pressure of the cutting chamber can be realized by inputting compressed air with an air pump, and the fan can be turned off when discharging.
This fish feed pellet extruder process method avoids controlling other factors that affect the degree of expansion, thereby reducing the need for manual operation, and at the same time, the controllability is stronger than other methods.
At present, this new fish feed pellet extruder technology has not been applied in China, but this technology is superior to the exhaust method in terms of density control of extruded products and operation and use, and is a new direction for the development of extruded technology.
(4) Controlling the opening rate of the template. By changing the opening rate of the discharge template, the pressure difference before and after the template can be changed, so as to achieve the purpose of controlling the density of the product. The hole is blocked.
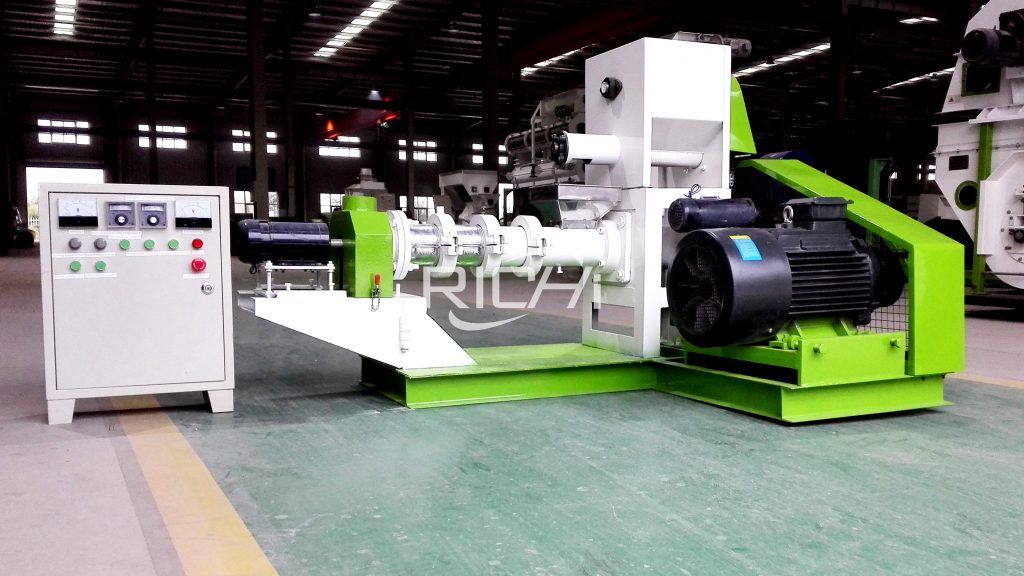
2. Automatic control of fish feed extrusion process
The automatic control of the fish feed pellet extruder extrusion process refers to the rapid and precise control of the process parameters by equipping the extrusion equipment with a computer-aided control system.
The application of automatic control technology in the fish feed pellet extruder puffing process can not only improve work efficiency, but also improve product quality stability. Models of automatic control at home and abroad
There are studies on all sides. The automatic control technology of the fish feed pellet extruder puffing process has made great progress, and a visualization control system of the puffing process has been developed. The extruding system of fish feed pellet extruder based on FIX industrial configuration software realizes the visual control of the extruding process.
The sensor can be used to conduct on-site detection and feedback on the operating parameters of the fish feed pellet extruder, automatically adjust the relevant working parameters of the floating fish feed pellet machine, and realize various preset by the operator.
Working parameters, with formula storage, report printing, alarm, dynamic display and recording of working parameters. Foreign computer automatic control technology has already been applied in the field of feed processing.
In the entire fish feed pellet extruder process, it has been developed from a single computer control system to an advanced automatic control system, which can display color images in the central control room, computer program control and communication network for floating fish feed making machine operation, it can complete all production procedures without unmanned operation.
In general, the automatic control of puffing in feed processing abroad has been developing towards the direction of combining with product quality.
While the introduction of computers in my country is mainly to solve the problem of production automation, only focusing on the monitoring of equipment operation in the production process and the control of stand-alone equipment. It has not played its due role in improving product quality and other aspects.
3. Energy saving in extrusion process
The problem of energy saving and consumption reduction is the research focus in the fish feed pellet extruder extrusion process.
At present, it is mainly through the research of low energy consumption processing technology and the influence of main process parameters on energy consumption, and the establishment of corresponding mathematical models to achieve the purpose of energy saving and consumption reduction.
In order to reduce the energy consumption in the fish feed pellet extruder puffing process, some domestic feed manufacturers mainly take measures from the process. For example, in the production process of suckling pig feed, the corn raw material used is not full puffed material, but part of the puffed material and part of the conventional material.
In the later fish feed pellet extruder granulation process, processes such as expansion and low temperature granulation are used to ensure that the energy consumption per unit product is reduced.
From the above analysis, it can be seen that it is still a bottleneck problem how the process parameter research in the fish feed pellet extruder puffing process can be embodied in reducing energy consumption and can be realized in actual production.
4. Application of extrusion in floating fish feed processing
In recent years, the application of fish feed pellet extruder extrusion technology to feed production is an epoch-making leap in feed production technology. The main advantages of extruded granulation:
The processing temperature is high and the moisture content is large, and the material can be fully matured and degraded. The pellets are of good quality and the feed titer is high;
The adjustable range of pellet density is large, which can adapt to the requirements of various feeding objects and different feeding environments.
(1) Puffed suckling pig feed
The important indicators of suckling pig feed are hygiene and maturation to prevent suckling pigs from diarrhea. The raw materials are treated with high temperature and high pressure, on the one hand, it kills pathogenic bacteria, on the other hand, the starch material is fully cooked, and the soybean protein is denatured and detoxified, so that the material is easy to digest and absorb. Gelatinized starch can stimulate the production of lactic acid in animals and enhance the antibacterial ability of animals.
(2) Extruded aquatic feed
The aquatic feedl is extruded and granulated by fish feed pellet extruder, which improves the quality of the product from all aspects.
①Improved feed titer. Extrusion ripens the starch, which is important for fish as raw starch is difficult to digest. The starch is cooked, the cohesiveness of the material is improved, and the forming effect is good. On the premise of ensuring the quality of pellets, the formula can be adjusted to reduce costs.
②The floating time of pellets in water is controlled by the density of pellets, and the density is determined by the degree of puffing by fish feed pellet extruder.
Therefore, by adjusting the formula, adjusting the variety and content of starch and binder, and adjusting the process parameters, that is, adjusting the moisture, pressure, temperature, etc., extruded pellets with different densities can be produced.
(3) Puffed chicken feed
The formula of chicken feed contains high starch material and 15%-20% protein material at the same time. For this proportion, no matter the dry floating pellet machine or the wet floating pellet machine, the technological performance is better.
Experiments have shown that puffing can improve the digestion and absorption rate of feed for chickens. Extruded chicken feed, because of its small bulk density, can reduce chicken feed intake, avoid obesity, and improve egg production.
(4) Puffed cattle feed (urea puffed corn)
Ruminants such as cattle and sheep can convert non-protein nitrogen (such as urea) into animal protein. The key to adding urea to feed is how to control the addition amount, uniform feed intake and urea decomposition rate. Urea-expanded corn solves these problems most effectively.
The urea, corn flour and additives are mixed in a certain proportion and then enter the floating pellet machine, the corn flour is expanded, and the gelatinized starch and urea form a coating structure. Urease inhibitors inhibit the activity of urease. It inhibits the release rate of ammonia after urea decomposition from two aspects, and avoids ammonia poisoning caused by excess ammonia.
(5) Rice bran preservation treatment
Fresh rice bran contains very active lipolytic enzymes, which can quickly decompose the oil contained in rice bran into free lipids
Fatty acid and rancidity, so the storage performance of fresh rice bran is extremely poor. The rancid and spoiled rice bran not only reduces the oil yield, but also affects the growth and development of livestock and poultry if fed as feed.
Therefore, fresh rice bran must be kept fresh in time. Extrusion, high temperature, high pressure and high shear can inactivate lipase and prevent rancidity and deterioration. Extrusion has become a new pretreatment process in rice bran oil production.
(6) Detoxification of oilseed meal protein
In addition to soybean cake (meal), the cake (meal) obtained from rapeseed, cottonseed, sunflower seed, castor and other oilseeds also contains a certain amount of protein, which is an excellent source of feed protein. However, various oil cakes (including soybean meal) cannot be directly used to formulate feed, because they all contain a certain amount of anti-nutritional factors or other harmful components.
Oil cake (meal) must be detoxified before it can be used. Detoxification methods include chemical and physical methods. Oilseed cake (meal) extrusion detoxification is a modern technology applied to oil cake (meal) treatment by extrusion technology.
(7) Feather puffing processing
Due to the existence of disulfide bonds and hydrogen bonds between feather polypeptide chains, the structure of feather protein is particularly stable, and animal digestive enzymes are basically unable to digest and decompose, so the feather extrusion technology has been developed.
After the feather is extruded and puffed, its disulfide bond is broken, the molecular structure is destroyed, and the digestive enzyme is easy to digest and decompose, and the digestibility is improved. The digestibility is related to the degree of degradation and extrusion temperature.
When the floating pellet machine extrusion temperature is high, the digestibility of the puffed feather product increases, but the amino acid content of the product decreases correspondingly, and the protein quality of the product decreases.
Feather meal has high protein content, but the amino acid is not balanced enough. In order to solve this problem, chicken viscera, chicken blood and feathers can be mixed and processed into intestinal feather meal.
Fish feed pellet extruder extruding technology is a feed processing technology developed at the end of the 20th century. Pressure cutting has a good effect on controlling the density of extruded products, providing a new method for processing high-demand aquafeeds.
The use of waste steam and waste heat for conditioning makes the machine more environmentally friendly and adapts to the trend of the times. Extrusion technology of fish feed pellet extruder is widely used in aquatic, swine and ruminant feeds, which has a significant effect on changing feed quality and reducing costs.
With the development of fish feed pellet extruder extruding technology, more in-depth research is needed on how to accurately control the expansiveness and extruding quality of extruded feed, and improve the automation of extruding.