(1) The temperature and time at which the poultry feed pellet making machine itself is connected to the steam, as well as the ambient temperature. The working principle of the poultry feed pellet processing machine is: use steam to supply, and then add material to ensure the temperature of the pellet. Where possible, heating is provided in the production workshop to ensure that the poultry feed production machines and production personnel work at normal temperature.
(2) Lubricating oil injected into the poultry feed pellet making machine. In the cold season, due to the low temperature, the grease of the particle feeder may solidify, making it difficult to refill the grease. Moreover, the low temperature may also cause the oil supply of the lubricating grease to be interrupted. Eventually wear is likely due to lack of oil.
(3) Dilution of grease. Using methods such as mechanically assisted oil injection, artificial heating, and oil dilution, small-scale poultry feed making machine grease liquefaction can be realized.
(4) Clean the studio of the molding wheel of the poultry pellet feed forming machine. After each operation, the extrusion table of the molding wheel of the poultry feed machine must be strictly cleaned to prevent the extrusion studio from freezing due to excessive humidity and low temperature, which will affect the normal operation of the small and medium-sized poultry feed pellet making machine.
(5) Timely maintenance and reasonable maintenance of the poultry feed pellet making machine. The maintenance and maintenance of poultry feed pellet making machine is very important. In this regard, try to carry out regular maintenance on time and troubleshoot before production. Replace damaged wearing parts in time to ensure high efficiency and high yield of pellets.
Especially in winter, if there is a little mistake, the poultry feed pellet making machine will appear abnormal. Therefore, all major users must do a good job in maintenance and maintenance in winter.
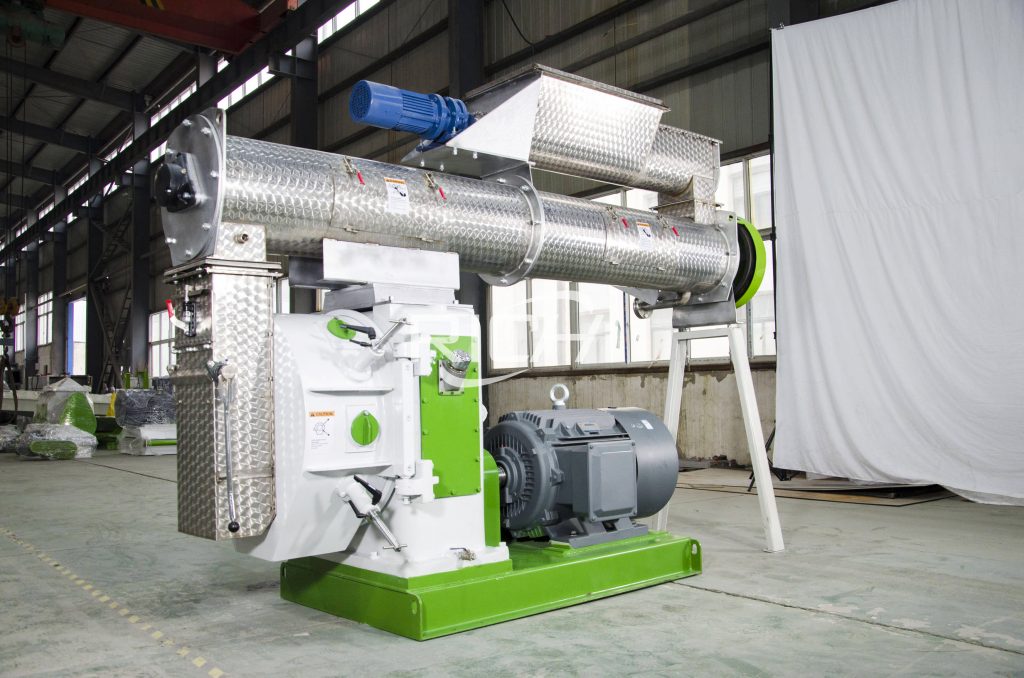
What equipment is the compound feed produced?
(1) Premix: It is made by mixing 90% carrier (corn meal, bran, husk meal, etc.) and 10% additives, accounting for 0.5~5% of the complete feed. Therefore, the additive with a small amount must be mixed with the carrier first, and then mixed with other feeds to achieve uniform mixing. Although the content of this feed is not high in the complete feed, it has a great effect and the production conditions are relatively strict.
Therefore, the large and medium-sized feed factories are generally used for the production of mixed feed without mixing workshops, and the small poultry feed factories directly purchase the products of the above-mentioned factories, in order to simplify the work and poultry feed machine.
(2) Concentrated mixed feed: It is made by pre-mixing carrier, protein feed and additives. When using, the feed needs to be diluted to 5~50% as full-price compound feed. Concentrate processing plants are often built in areas where protein feed resources are concentrated.
(3) Complete compound feed: It is made by mixing energy feed and concentrated mixed feed and diluted in 2). This product can meet all stages of the growth of livestock and poultry. The full-price compound feed factory for direct processing of feed raw materials is generally established in large and medium cities or important traffic areas.
However, those poultry feed mill factories that use concentrated beverages to produce full-price beverages can also have relatively simple processes and equipment, and are mostly located in feed factories in small livestock farms.
(4) Formulated concentrated feed: It is formulated with energy feed and protein feed. It is suitable for small-scale farming in my country and is fed with silage. This type of beverage has less stringent requirements for adding trace amounts, so it can simplify the production process, reduce investment and reduce costs. In my country, feed factories are the main ones, and most of them are built near grain and oil processing factories or warehouses near small towns.
What are the cleaning methods of the feed pellet machine?
Common cleaning methods in the world: The most common cleaning method is a three-step cleaning method based on alkaline cleaning, pre-cleaning – chlor-alkali cleaning – post-cleaning, and the frequency of pickling is determined according to water hardness.
This cleaning method is widely used in most European countries and Asian countries, such as the Netherlands, where it is the standard cleaning method for pastures. However, the traditional cleaning method in Denmark is: pre-cleaning – alkaline cleaning – cold water cleaning – acid cleaning, with pure cold water before milking.
The most common cleaning steps in the U.S. are: pre-rinse – caustic – pickling, sanitizing before milking. Pickling is a common cleaning method in New Zealand, namely boiling water with acidic cleaning agents, cold water and periodic alkaline cleaning.
In conclusion, what cleaning method for poultry feed pellet making machine to use mainly depends on the customs and legal requirements of different countries, as well as the energy costs required to heat the water, cleaning costs and cleaning conditions.